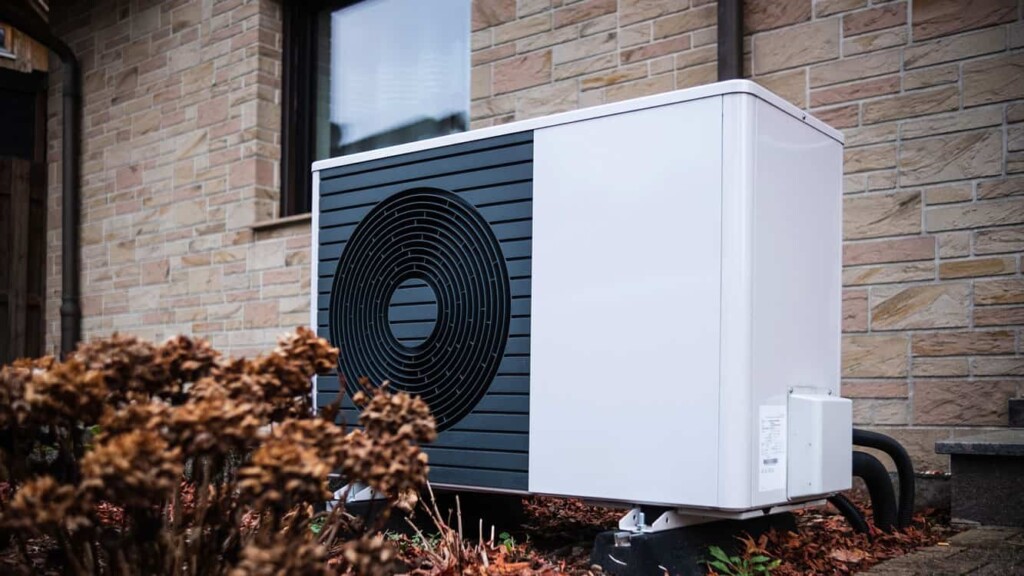
Real-World Performance of Mixergy and Heat Pumps
A quiet revolution in the heating space is taking place as two tech frontiers collide: 1) the advent of domestic heat pumps and 2) the emergence of remote monitoring and the Internet of Things (IoT).
At the centre of this collision is an online community called Heat Pump Monitor. Their mission is to observe, report and compete on system performance across heating installations throughout the UK. Their website provides live system operating data from each heat pump installed, and this service has provided fascinating insights into how Mixergy interacts with the real world.
The following diagram shows how the system works:
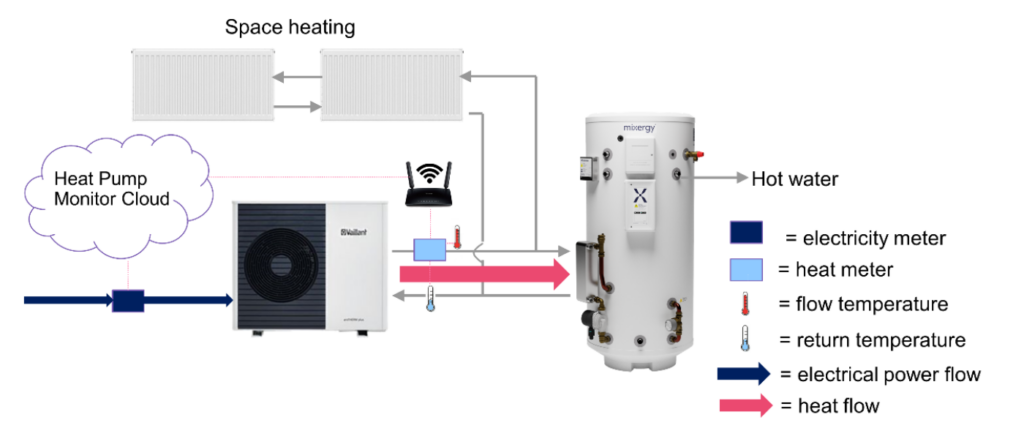
The monitoring system works by measuring the electrical power going into the heat pump and the heat flowing out of the flow and return pipework to the heating system.
The heat flow is calculated using a heat meter. This works by measuring the flow rate out of the heat pump alongside the temperatures in both the flow and return. The meter then performs the following calculation with these parameters to determine the thermal energy output:
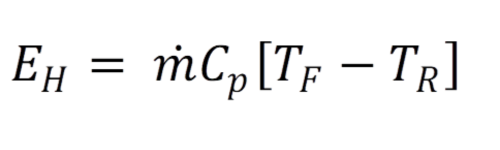
Where EH is the thermal energy flowing out of the heat pump (in watts), m is the flow rate (converted to kg/sec), Cp is the heat capacity of water, a fixed value of 4,180 Joules/°C, TF and TR are the flow and return temperatures in °C. The electrical power Ee is measured using an electricity meter, completing the picture on COP, which is:
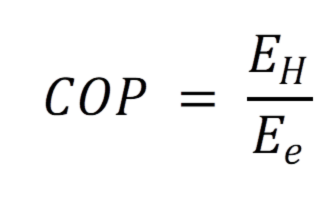
Many of the Heat Pump Monitor contributors aim to be ‘top of the sCOPs’ where the ‘s’ prefix stands for ‘seasonal’. The seasonal COP is simply the average performance of the whole heating system (space and hot water) over time.
The simplest way to get to the top of the sCOPs is to keep things cool, meaning always keeping the system loop temperature as low as possible. This can be achieved by:
- Designing a heating system with large surface areas (big radiators and underfloor heating)
- Having very good heat transfer between the system loop and the hot water cylinder through a large coil or well-designed plate heat exchanger arrangement
- Run the hot water cylinder at a low temperature (without creating a sanitary hazard)
- Running the heat pump in a reduced power mode or ‘eco-mode’ allows energy to be transferred with a lower return temperature back to the heat pump. Imagine pushing current down a resistive wire; the more current (heat) you push, the larger the voltage you need (or temperature from the heat pump)
- Ensure that the highest possible flow rate can be achieved from the heat pump to minimise the temperature needed to ‘push’ thermal energy through the system.
Keeping things cool ensures that we are getting the best performance within the thermodynamic limits of a heat pump, which are determined by a famous equation from the father of thermodynamics, Sadi Carnot:
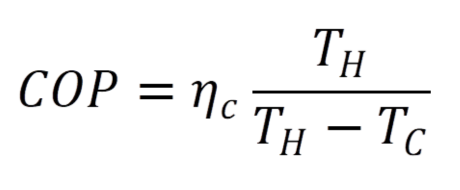
Where COP is the Coefficient of Performance, nc is the engineering efficiency factor, which captures all sorts of things ranging from power losses in the heat pump’s inverter, flow losses within the refrigerant loop, compressor heat losses, energy consumed by the air source fan and so on. TH is the temperature at which energy is being dispatched (in the case of the heat pump, this is the same as the flow temperature TF). Meanwhile, TC is the outdoor temperature from which the heat pump is sourcing thermal energy in the first place.
Things get a little complex when trying to isolate the performance of individual components, such as the hot water cylinder. This is due to the many variables contributing to overall performance (as discussed above).
However, with the wonders of big data, we can begin to understand heat pump performance over time in the field by isolating hot water heating events from the rest of the space heating system.
One example directly from Heat Pump Monitor for a Mixergy system is provided below, where a Mixergy cylinder’s performance was tested during a full re-heat event:
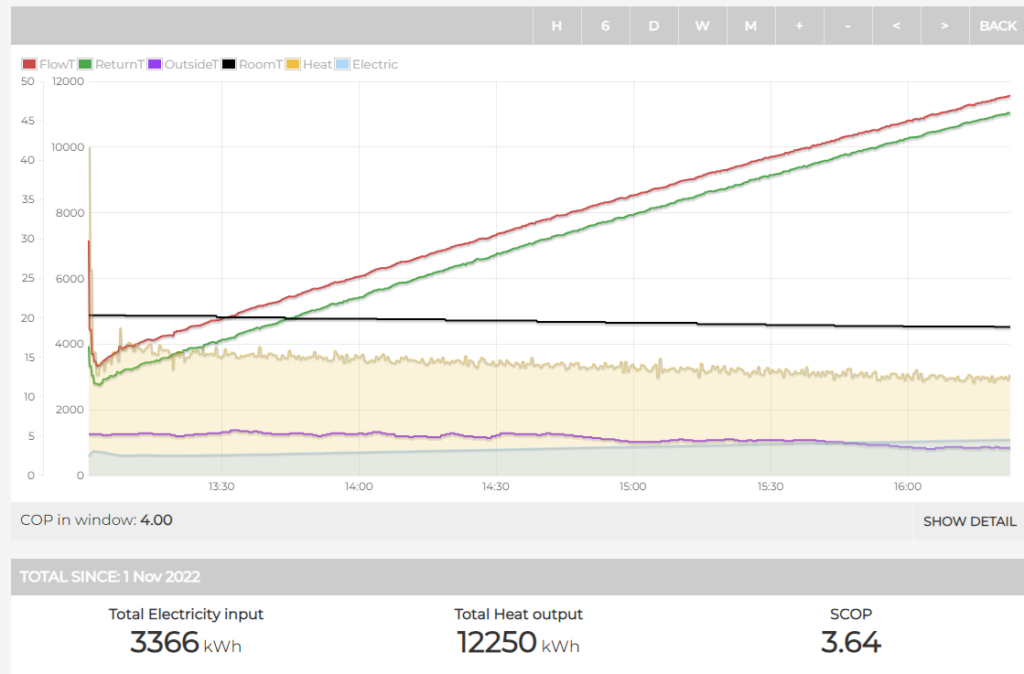
At Mixergy, our IoT system allows us to cross-reference the data from the Heat Pump Monitor with measurements from within the Mixergy cylinder.
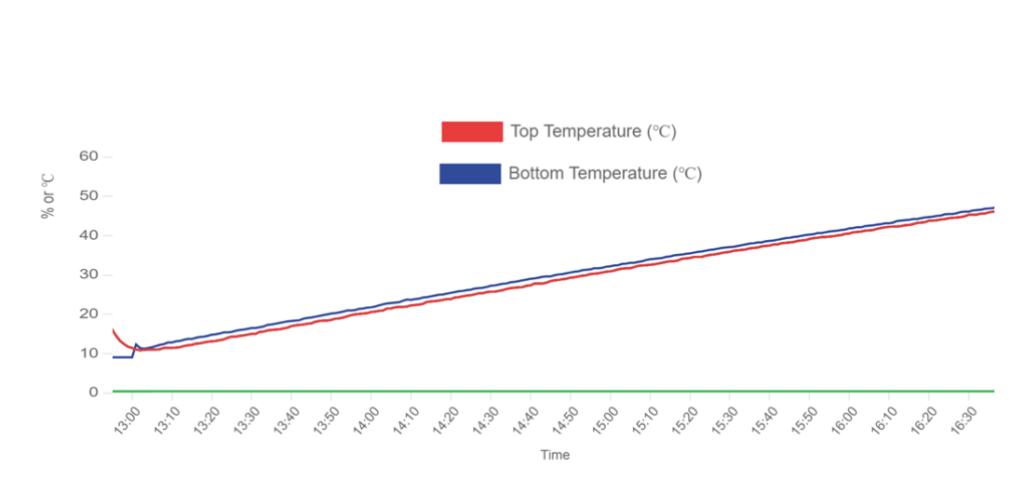
A full reheat test is useful since we can observe the relationship between COP and cylinder temperature at each point in time through the Heat Pump Monitor’s very helpful ‘COP in window’ report, which allows you to provide an average COP value over any timespan you like. In this instance, the Vaillant system with Mixergy cylinder delivered an average COP of ~4 from fully cold up to 45oC. This dropped to 3.6 as the temperature climbed to its final target of 51oC.
One of the key advantages of the Mixergy cylinder is that we always exchange thermal energy with the coldest part of the cylinder at all times via a plate heat exchanger. This keeps things cool whilst keeping the COP high. This is true irrespective of the Mixergy cylinder’s state of charge.
On the other hand, a coil-based cylinder suffers when reheating from a partial state of charge because its surface area is effectively ‘locked out’ by the thermal energy already present at the outset of the heating event.
You can read more about this in a focussed blog article on this subject in our article Plate heat exchanger vs Coil: the great debate.
Over time, as we build up a better picture of real-world data, we can begin to get a fuller understanding of this benefit. However, we can already see the poor COP values that coil cylinders can suffer from:
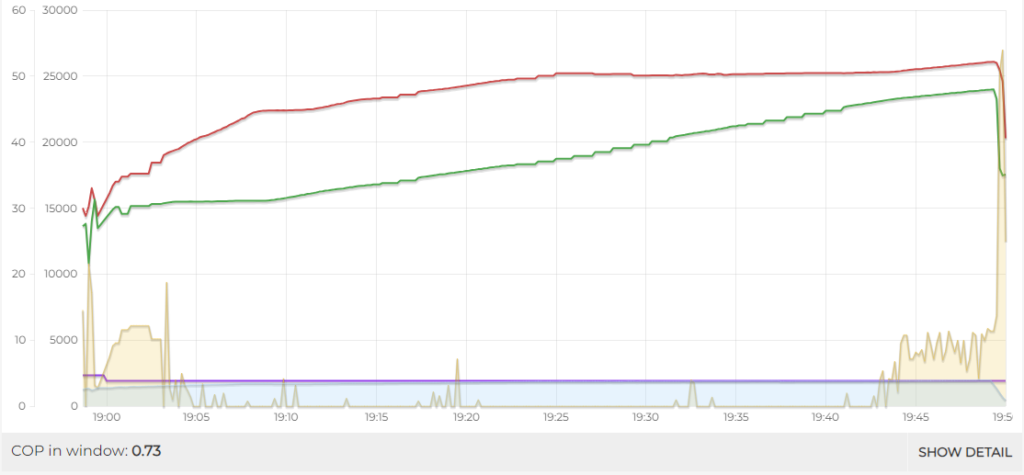
The benefits of a Mixergy cylinder don’t stop there. In addition to delivering the highest COP during partial reheats, the Mixergy cylinder also features the following:
- State of charge monitoring so that you always know if there’s enough heat to cover the day
- The ability to set an intelligent heating schedule driven by state of charge rather than a single temperature set point (this means we can wait until the right time to fully reheat the cylinder rather than at an arbitrary point in time, depending on where the cylinder probe is located)
- Future-proofing through connected control so that the system can work most effectively with smart tariffs
We want to thank the team behind Heat Pump Monitor for making real-world, real-time data available.
Alongside this, we undertake testing in our lab within an environmental test chamber (this helps us to create repeatable tests in a controlled environment (which we will outline in a future article). Combining these tests with the field data provided by Heat Pump Monitor is truly invaluable when developing products in the home.